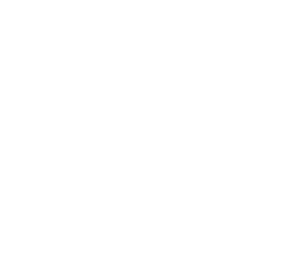
A diferença entre Granulação Via seca e Úmida
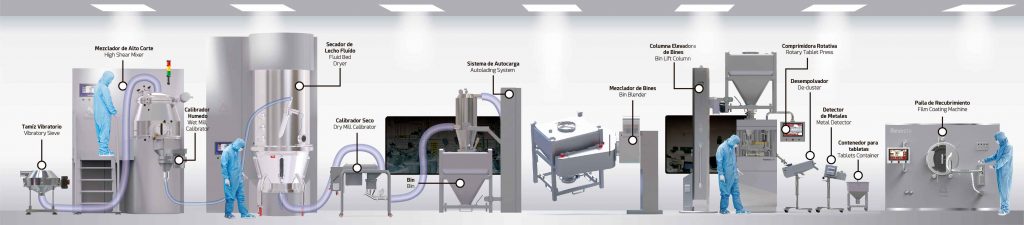
A diferença entre Granulação Via seca e Úmida
Os desafios na produção de uma indústria farmacêutica são infindáveis, sabemos que todos os envolvidos possuem grande parcela de contribuição para que tudo saia corretamente nos conformes esperados, mas para tal resultado positivo é necessário o verdadeiro entendimento do que é melhor para cada produto de acordo com cada característica pontual, afinal de contas estamos falando de produtividade e de qualidade.
Atualmente existem diversas tecnologias para granulação e devido ao tamanho da importância que este processo exerce na produção farmacêutica de sólidos, este artigo foi produzido para trazer orientações e elucidar sobre todas elas, assim a visão dos processos ficam mais claros e as decisões ficam mais fáceis de serem tomadas, como por exemplo: qual processo utilizar em um determinado produto ou até mesmo qual é o melhor equipamento para tal processo.
Aproveite o artigo e nos conte o que achou ao final da leitura.
Tecnologia de Granulação
Conforme acabamos de falar: o processo de granulação na produção farmacêutica exerce uma importância significativa para que tudo ocorra bem no processo de compressão, afinal de contas o produto final deve manter a qualidade, mas não pode perder a produtividade. Essa importância toda da granulação se dá pelo fato de que os compostos farmacêuticos mais finos necessitam da granulação para que sua fluidez seja melhor e as propriedades façam com que o processamento da compressão seja eficaz, compreender os princípios das opções de granulação e seus prós e contras é essencial para evitar resultados indesejados (tais princípios e opções estão neste artigo para você).
Atualmente existem três processos de granulação mais comuns para a produção de formas sólidas que são: a granulação via úmida, a granulação via seca e a combinação direta, neste artigo trataremos da granulação via seca e úmida.
Vamos ao que interessa!
Granulação Seca
Com toda certeza esse processo é mais rápido e “econômico” pois evita diversos passos para finalizar o grânulo, mas não se engane! Nem todos os fármacos comprimem com eficiência por meio deste processo – por isso você precisa entender qual é o melhor processo pensando no seu produto final.
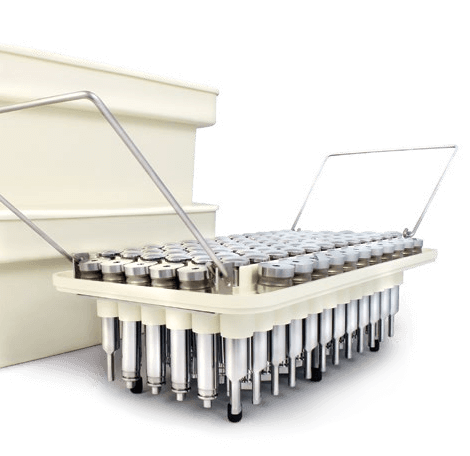
O detalhe é que este processo é utilizado para formar grânulos sem usar uma solução líquida, isso se o produto a ser granulado for sensível à umidade e ao calor ou não compactar bem. A formação de grânulos sem umidade envolve compactação e redução do tamanho da mistura para produzir um blend granular, de fluxo livre e com tamanho uniforme. Assim, as partículas de pó primárias são agregadas sob alta pressão usando granuladores misturadores de oscilação ou alto cisalhamento. A granulação seca pode ser realizada de duas maneiras: ou é produzido um grande tablete em uma prensa maciça para compressão do tablete ou o pó é prensado entre dois rolos para produzir uma folha de materiais chamado de compatador de rolo.
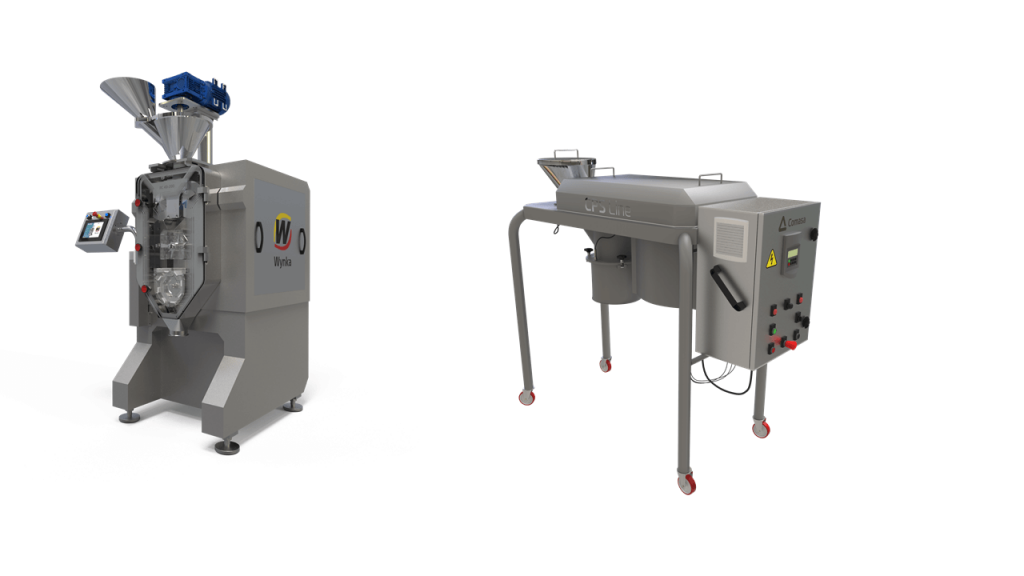
Quando uma prensa é usada para granulação seca, os pós podem não possuir um fluxo natural suficiente para alimentar o produto uniformemente na cavidade da matriz, resultando em diferentes graus de densificação. O rolo compactador (granulador-compactador) usa um sistema de alimentação que irá proporcionar um pó consistentemente uniforme entre os dois rolos de pressão. Os pós são compactados em uma fita ou pequenos pellets entre esses rolos e moídos por meio de um moinho de baixo cisalhamento. Depois do produto ter sido compactado adequadamente, ele pode então ser passado através de um moinho e finalmente misturado antes da compressão.
Granulação úmida
Neste processo o sistema é totalmente diferente, começando pela adição de uma solução líquida aos pós envolvendo-os em aglomeração para uma mistura de partículas de pó secos e primários usando um fluido de granulação. Este fluido contém diversos compostos importantes, mas se dentre eles o solvente estiver presente – você precisa saber que ele deve ser volátil, sendo volátil no momento da secagem ele será removido evitando problemas tóxicos posteriormente. Esses líquidos tipicamente incluem: água, etanol e isopropanol, isolados ou em combinação.
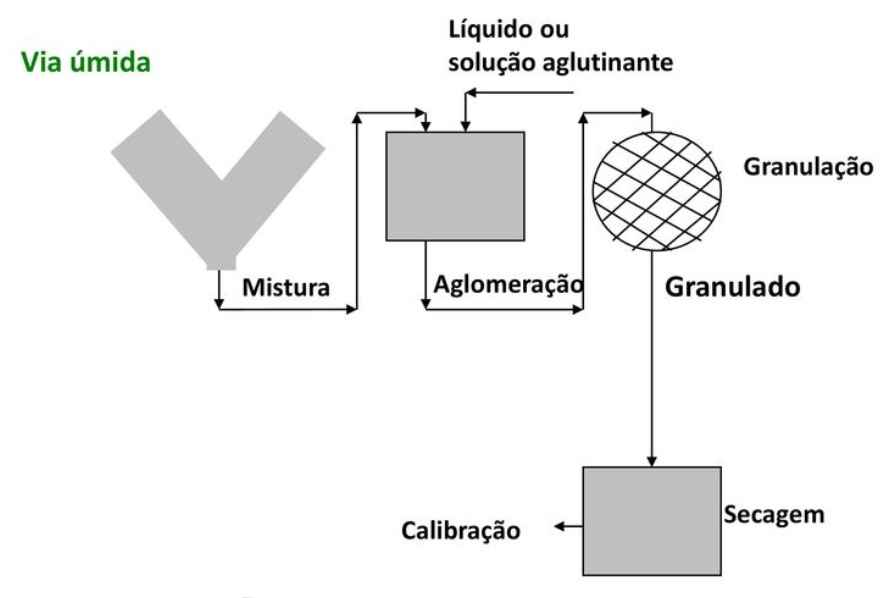
A solução líquida tanto pode ser de base aquosa, por sinal é a mais segura, ou de base solvente. A água misturada nos pós pode formar elos entre as partículas de pó fortes o suficiente para mantê-las unidas. No entanto, quando a água seca, os pós podem se separar. Portanto, a água pode não ser forte o suficiente para criar e manter um elo. Nesses casos, é necessária uma solução líquida que inclua um aglutinante. Uma vez que a água/solvente tenha secado e os pós tenham formado uma massa mais densa, a granulação é então moída.
Cada fármaco age de determinada maneira durante os processos, cada processo pode ser muito complexo ou muito simples, tudo dependerá das características dos pós e da tecnologia dos equipamentos.
No método tradicional de granulação úmida, a massa úmida passa por uma peneira para produzir grânulos úmidos que são posteriormente secos. No próximo passo os grânulos aglomerados são quebrados. Os solventes orgânicos são usados quando se processa medicamentos sensíveis à água, como uma alternativa para a granulação seca, ou quando é necessário um tempo rápido de secagem. Devido ao fato da compressão direta não ser a melhor tecnologia para muitas substâncias ativas, a granulação úmida ainda é um método mais utilizado pelas indústrias farmacêuticas. Mesmo que a substância ativa seja sensível à hidrólise, os equipamentos modernos (um leito fluidizado, por exemplo) eliminam todos os problemas com a granulação úmida.
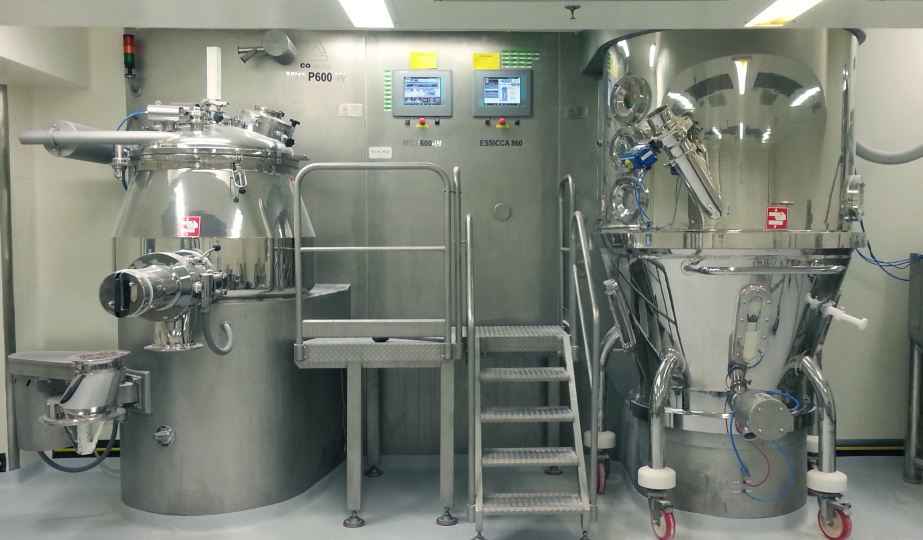
A granulação úmida envolve a produção de grânulos pela adição de aglutinantes líquidos para a mistura dos pós. Tanto o processo de Compressão Direta Contínua como o de mistura contínua para granulação seca envolvem o carregamento individual e a alimentação precisa dos ingredientes farmacêuticos ativos (API ou IPA) e uma variedade de excipientes em um misturador contínuo.

Tecnologias de granulação
A Mederi Brasil possui marcas líderes de mercado para fornecer o que existe de mais inovador para o perfeito funcionamento dos seus processos, fora o serviço de apoio ao engenheiro, equipamentos para a sua produção apoiando o processo inteiro de fabricação com máquinas e ferramentais de ponta e suporte ao cliente.
Conte conosco para apoiar os seus projetos com inovação, performance e produtividade, claro, superando todas as expectativas de qualidade.
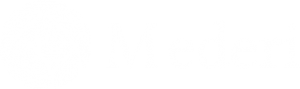
Somos especialistas em equipamentos para a Indústria Farmacêutica.
Entre em Contato
Avenida São João, 2375, Sala 1010 – São José dos Campos – SPCEP 12242-000
(11) 98470-3068
Seg – Sex: 9AM – 17PM
mederi@mederibrasil.com