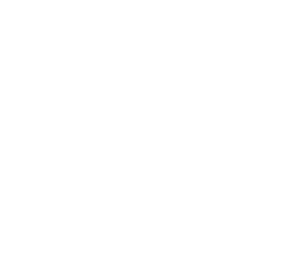
COMO REDUZIR CUSTOS COM PROBLEMAS DE SCALE-UP?
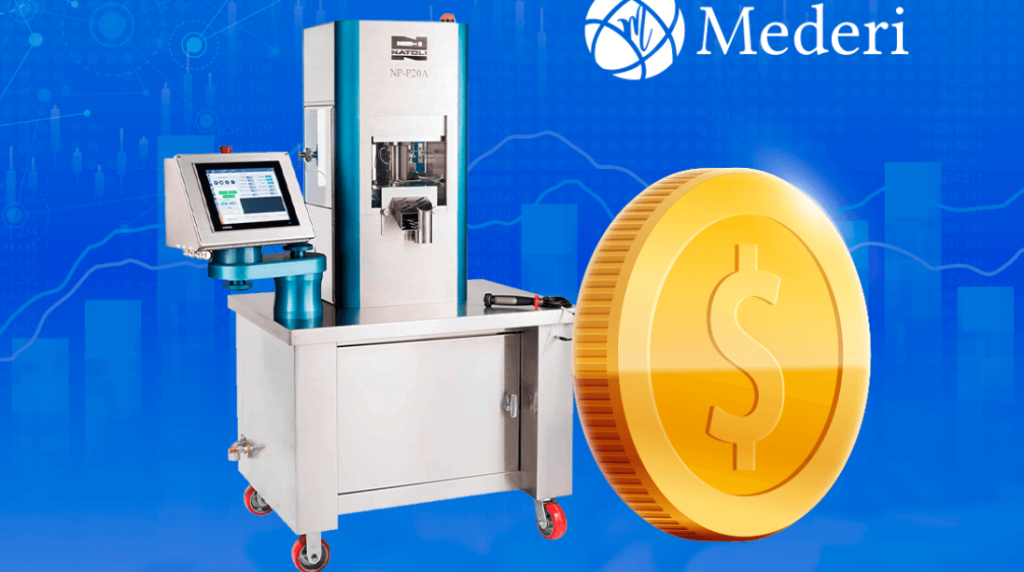
Ao dimensionar uma nova formula de medicamento do setor de P&D para a produção, normalmente há dificuldades no que diz respeito ao scale-up e desempenho da formulação em diferentes níveis de produção. Problemas com capping/lamination e sticking/picking são os primeiros a serem identificados quando uma nova fórmula é introduzida a um nível de compressão necessária para atender a demanda do mercado.
Fabricantes de ferramentais para compressão são questionados frequentemente sobre a razão pela qual os ferramentais fazem com que uma fórmula gere comprimidos com defeitos óbvios e inaceitáveis. Apesar de aprovar o design do comprimido, o gerente de produção se depara com correções que não envolverão discussões com órgãos reguladores – internos ou externos. Frequentemente os técnicos nas cabines de compressão terão a liberdade de operar as condições de compressão, em todas as combinações possíveis, tentando corrigir o problema. Depois de tentar diversas misturas na pré compressão, compressão final, velocidade do alimentador, e velocidade do rotor, a falha óbvia deverá estar nos ferramentais.
O problema com esse pensamento é que ferramentas de compressão possuem diversas variáveis que não são consideradas regularmente e, certamente, não são testadas antes de se estudar sobre scale-up. Essas variáveis nas ferramentas são normalmente examinadas quando há um problema como aderência (sticking). A triste realidade é que a formulação do medicamento deveria ser avaliada através de uma série de experimentos simples, para determinar quais seriam os problemas potenciais antes de ser registrada em órgão regulatório. Acelerar a inserção de um produto no mercado pode trazer algumas lições caras e doloridas se a formulação falhar em atender expectativas de capacidade e rendimento da fabricação.
Para examinar as fórmulas para possíveis problemas com scale-up, os simples experimentos a seguir devem ser considerados para caracterizar performances de formulações: perfil de compactação e taxa de sensibilidade à deformação. Um perfil de compactação oferece ideias sobre o desempenho do pó sob compressão. O teste mais simples é a compressão do pó em diferentes forças e testes na resistência a quebra do comprimido. Uma abordagem alternativa é padronizar a pressão da ponta do punção ao invés de usar apenas a força de compressão. Um estudo do pó utilizando uma taxa de pressão típica na indústria farmacêutica de 50 MPa – 300 MPa permite uma simples comparação de comprimidos de diversos tamanhos usando a mesma formulação. Um perfil típico é mostrado na figura 1 para uma quantidade de fórmulas que foram comprimidas em uma compressora de estação única. As formulações possuem alta carga de medicamentos. Uma formulação é feita por granulação seca enquanto a outra é feita via granulação úmida. Um comprimido robusto tem uma força de tensão de 1 a 2 Mpa. Nenhuma das duas misturas testadas produz um comprimido aceitável.
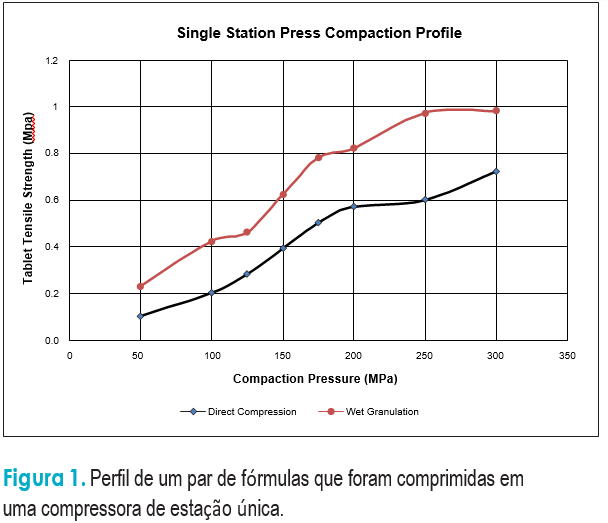
Movendo o processo de compressão para uma compressora rotativa resulta em dados diferentes. Como apresentado na figura 2, a fórmula via granulação úmida produz uma força de tensão com força de compressão adicional. Uma vez que a força de compressão atinge 150 MPa, um comprimido mais robusto é produzido. A granulação seca não irá comprimir com força suficiente, podendo produzir um comprimido que apresente problemas de capping em compressões maiores. Embora incomum, para registrar o medicamento de maneira ágil e eficiente fará com que alguns sigam diretamente para fórmulas de granulação seca.
Com informações indicando que compressoras de uma única estação irão produzir comprimidos de dureza aceitáveis, desintegração e dissolução, o registro estará em questão antes que testes em compressoras rotativas sejam realizados usando materiais da primeira etapa de do processo scale-up. A maioria das fórmulas não ignoram o rigor exigida durante os testes de scale-up; contudo, muitos supõem a respeito da capacidade de seus produtos na escala exigida para atender às demandas dos pacientes. Mudar para uma compressora rotativa maior de 40 a 70 estações de ferramentais altera significativamente a dinâmica do processo de compactação do pó como resultado de mudanças na velocidade geral do processo de compressão. Enquanto uma compressora maior é usada para atender as demandas de produção, conforme o diâmetro do rotor aumenta, a velocidade vertical do punção aumenta e o Dwell time diminui. A figura 3 ilustra os resultados do estudo da taxa de deformação simples. Para obter as informações apropriadas, a força de compressão é fixada e a compressora roda a diferentes velocidades . Para esta ilustração, a velocidade do rolo de compressão e a área plana da cabeça do punção foram usados para calcular o dwell time da compressão e é apresentado em unidades de milissegundos no eixo x. Para esta discussão, o Dwell time é definido quando os punções inferiores e superiores não tem movimento vertical.
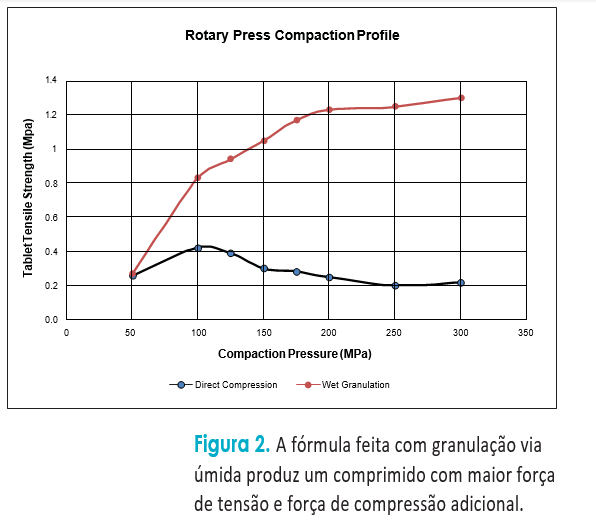
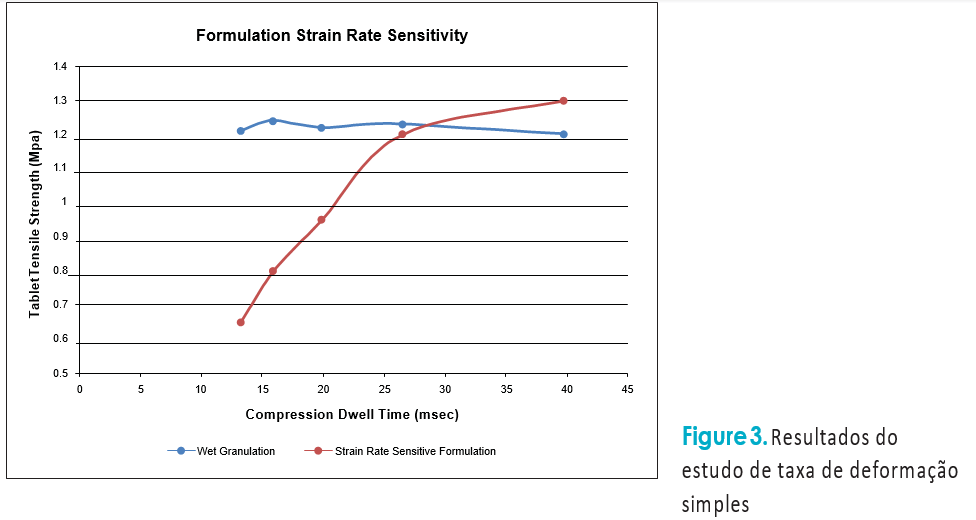
A granulação úmida é capaz de produzir comprimidos aceitáveis em todas as velocidades do rotor enquanto as fórmulas sensíveis à taxa de deformação exigem menores velocidades do rotor afim de produzir comprimidos aceitáveis. Este é um problema, pois as fórmulas sensíveis a taxa de deformação (granulação seca) não serão capazes de produzir tantos comprimidos por hora quanto a granulação úmida.
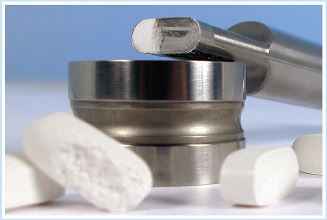
Enquanto esses testes podem ser fáceis de fazer, eles consomem tempo e custo no que diz respeito a custos de API. Então, o que o gerente de produção precisa fazer quando tiver que atender as necessidades de satisfação da gestão e tem uma fórmula de baixo desempenho? Discutir as opções com a fornecedora de ferramentais de compressão. Elas podem oferecer mudanças nas ferramentas que podem ser capazes de resolver ou, no mínimo, minimizar o problema.
Quando a sensibilidade à taxa de deformação é um problema e requer uma taxa de produção mais lenta para produzir comprimidos aceitáveis, então ferramentais com áreas planas da cabeça estendidas podem ser consideradas. Ferramentais tipo TSM-B e TSM-D podem ser modificados para aumentar a área plana da cabeça e promover um maior Dwell time com a mesma velocidade do rotor. Isso pode promover uma melhora na taxa de produção do comprimido ou eliminar pequenos defeitos ligados a falta de tempo de consolidação do pó.Às vezes, as fórmulas de um medicamento performam bem; contudo, após várias horas haverá problemas com material grudado no copo do punção ou no orifício da matriz. Existem várias causas para este problema. Sticking pode estar relacionado a temperatura e uma solução para o problema pode exigir o teste de um revestimento para o copo do punção para diminuir a adesão de pó. A geração de calor pode ser causada por partículas finas passando pelo copo do punção e entrando no orifício da matriz causando fricção excessiva e aumento da temperatura. O número de partículas finas passadas para o punção inferior podem diminuir ao reduzir a folga entre a ponta do punção e a parede da matriz. Além disso, uma ponta mais estreita pode ajudar a reduzir a fricção e uma ponta mais afiada pode ser mais eficaz na remoção do excesso de pó na parede da matriz.
O picking é uma condição que se refere a fórmula ficando presa nas letras ou números do logo ou identificador do comprimido. Problemas de picking são normalmente resolvidos por meio de modificações no relevo das letras ou utilizando configurações de copos compostos para melhorar a compressão nas áreas mais profundas do copo do punção.
A pré-seleção de letras ou números ou áreas isoladas bem como a redução dos cortes de gravação para algumas letras, muitas vezes aliviam os problemas de picking. Considere executar um lote teste de grande escala, incluindo estações de ferramentais com diferentes pré-seleções e afunilamentos, para identificar problemas de sticking e picking antes deles aparecerem. Algumas vezes, esses problemas surgem como cortesia, de pequenas mudanças em fatores ambientais ou variação na cadeia de suprimentos. Rodar um lote para teste antes pode fornecer mais entendimento sobre o processo e conhecimento sobre o design da formulação do produto.
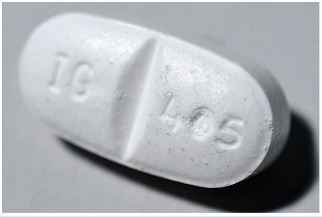
Outro problema encontrado ocasionalmente é a aparência do defeito nos comprimidos quando a produção é transferida para larga escala e a nova compressora tem a capacidade de pré-compressão enquanto o setor de P&D não tem. O ajuste adequado da pré compressão deve ser estudado detalhadamente antes de definir a escrita final para o comprimido. Para a formulação de um medicamento que possui uma carga elevada de API e configuração imprópria na pré-compressão pode ser um caminho para problemas de qualidade no comprimido. Os ativos são tipicamente cristais orgânicos que comprimem através de um mecanismo frágil. O excesso de força de pré compressão seguido a uma compressão final pode resultar na geração de uma quantidade significativa de cristais muito pequenos que não vão se consolidar da mesma forma quando uma força mínima ou nenhuma força de pré-compressão é utilizada. A função da pré-compressão é remover o máximo de ar possível no pó antes da compressão final. Em conjunto com matrizes cônicas, isso minimizará problemas com capping no comprimido.

A configuração adequada da pré-compressão requer que o mecânico de compressão remova todas as compressões principais e anteriores. Encha a compressora com pó e manualmente rode-a enquanto adiciona força de pré-compressão. Adicione essa força até o comprimido seja ejetado da matriz. Esse comprimido deve parecer normal, mas pode se desfazer facilmente. A este ponto, a pré-compressão é configurada e a compressão final é adicionada até atingir a dureza desejada para o comprimido.
O uso de guia de enchimento adequada é frequentemente esquecido durante o processo de scale up. Regularmente um comprimido é utilizado com qualquer guia de enchimento instalada. Se as guias forem reguladas para atingir o peso e dureza desejados para o comprimido, está tudo bem. Isso funciona até um operador identificar excesso de pó se acumulando na matriz porque muito pó está sendo empurrado pela guia de enchimento. O pó reciclado retorna ao processo e é misturado mais uma vez com o material virgem. Dependendo da distribuição do tamanho da partícula e a tendência dos cristais API se fraturarem, uma fração da mistura agora é menor e pode afetar a qualidade dos comprimidos. As partículas menores podem mudar a dinâmica de enchimento da matriz, assim como contribuir para a perda de partículas pequenas no espaço entre a ponta do punção e o orifício da matriz.
Partículas muito pequenas (<10 µm) podem começar a se acumular em arranhões na superfície do copo do punção, que é o primeiro passo para problemas de sticking. Guias de enchimento impróprias também podem afetar na variação do peso de enchimento e dureza do comprimido quando diferentes velocidades de compressão são utilizadas. Diferentes velocidades de compressão irão exigir ajustes na velocidade do alimentador para atender as propriedades físicas do comprimido. Estudos feitos como parte do desempenho de um lote com scale-up e feitos com uma guia de enchimento inapropriada podem ser comprometidos se a guia de enchimento for alterada em determinado momento. Assim como, o ajuste de velocidade do alimentador pode não ser feito de forma tão intuitiva como se espera. Se modificadas as pás de alimentação utilizadas durante o desenvolvimento para resolver problemas com o enchimento da matriz de uma formulação que é aderente por natureza, o mesmo tipo de pás de alimentação será necessário para uma produção em larga escala. Reciclagem do excesso de pó, escolha da guia de enchimento incorreta, pode afetar no controle da variedade de peso do comprimido e mistura uniforme e diferentes velocidades de compressão e velocidade do alimentador. A seleção da guia de enchimento adequada é um passo simples, normalmente ignorada, mas que pode prevenir problemas no futuro.
Para os profissionais de desenvolvimento que iriam preferir minimizar as etapas desde o conceito até o registro da forma de dosagem, as sugestões anteriores provavelmente descrevem desvios indesejáveis de tempos e recursos. Essas recomendações devem ser valiosas para aqueles que desejam minimizar os desvios nas etapas de desenvolvimento. Para um sistema perfeito, o trabalho é independente do caminho .
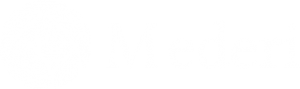
Somos especialistas em equipamentos para a Indústria Farmacêutica.
Entre em Contato
Avenida São João, 2375, Sala 1010São José dos Campos – SPCEP 12242-000
(11) 98470-3068
Seg – Sex: 9AM – 17PM
mederi@mederibrasil.com