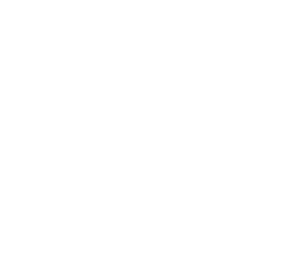
Princípios do Design do Blister
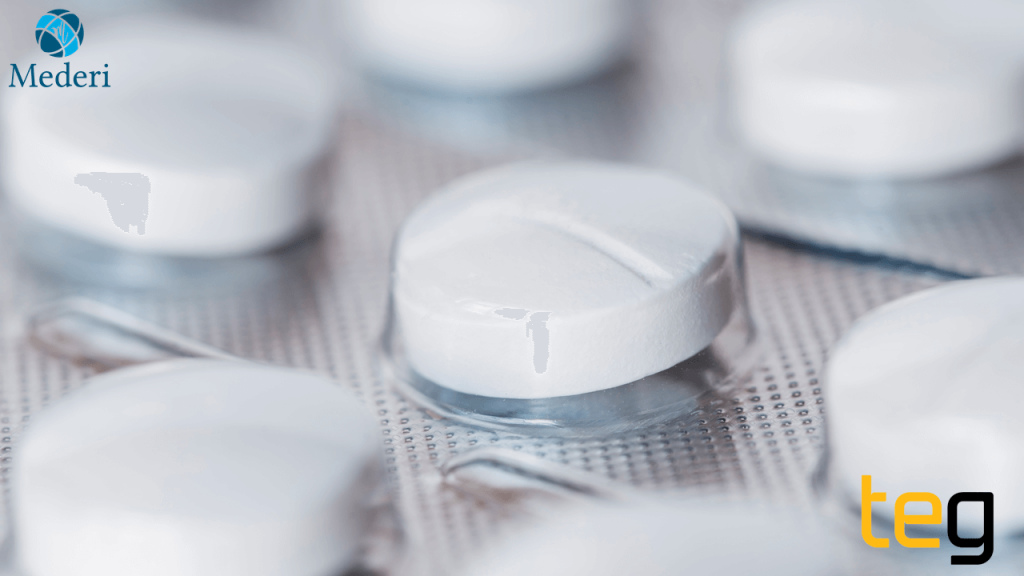
Os princípios do design do blister
A embalagem de um medicamento é o resultado do compromisso com a qualidade do produto final disponibilizado para o consumidor. Para que um blister seja eficiênte, dentro das exigências, ofertando a barreira de proteção necessária e que performe bem na emblistadora, é necessário que vários profissionais e diversos setores estejam engajados no projeto e tenham atenção em detalhes importantes do processo.
O design do blister é um detalhe importante no setor de embalagens primárias, pois ele interfere diretamente desde a barreira de proteção do comprimido até a formação do material no equipamento de produção, sendo assim, aqui temos um artigo muito rico em informações para você consultar sempre que precisar. Continue lendo e descubra várias dicas para o seu desenvolvimento de embalagens.
Aqui veremos sobre a geometria básica da cavidade, pré-formação (plug assist), vedação mínima, rigidez do blister e desing do nervo.
Então, vamos iniciar.
GEOMETRIA BÁSICA DA CAVIDADE
Todos os materiais de formação se comportam de maneira diferente e, portanto, nem todas as formas geométricas fornecem bons resultados.
Em geral, as geometrias mais esféricas levam a filmes mais espessos e uniformemente distribuídos.
Quando precisamos trabalhar com uma cavidade mais esférica, normalmente temos que pensar em detalhes que envolvem:
• Incorporar um generoso raio de filete de canto (Corner Fillet)
• Aumentar o filete de flange (Flange Fillet)
• Aumentar o ângulo de inclinação (Draft Angle)
• Minimizar a profundidade (Depth)
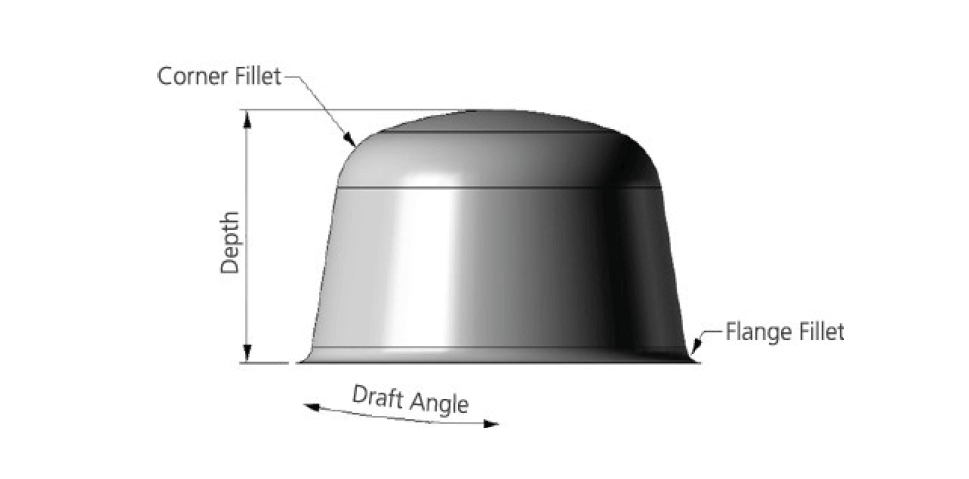
Porém, existem alguns detalhes que você deve observar aqui e ponderar algumas informações. Pense nos seguintes pontos:
1. O tipo de máquina: Existem limitações em algumas máquinas, formando profundidade, Blister Guiding, máquina contínua com rolos de vedação de pequenos diâmetros;
2. O tipo de sistema de alimentação: Se a bolsa é muito grande e usamos um alimentador vertical ou universal, dois produtos poderiam caber em uma única bolsa;
3. O tipo de material de formação: Existem ângulos mínimos de inclinação para diferentes materiais e formatos de bolsas.
4. O Espaço disponível no blister: Em um caso de harmonização, por exemplo, o tamanho da bolsa do blister é fixo, portanto, pode não haver espaço sobrando para aumentar a área de cobertura de uma cavidade;
5. A vedação mínima: Ao aumentar a área de cobertura da cavidade, você pode estar reduzindo a área da vedação, resultando em uma falha nesta vedação.
Design da bolsa padrão
Devemos usar um raio em vez de um chanfro na entrada da cavidade (Flange Fillet ). Os chanfros aumentam o afinamento da parede e podem diminuir a barreira da cavidade. Recomenda-se um raio de 0,5 mm e, se a largura da flange de vedação permitir, use um raio de 1 mm.
Na figura abaixo você pode ver a comparação:
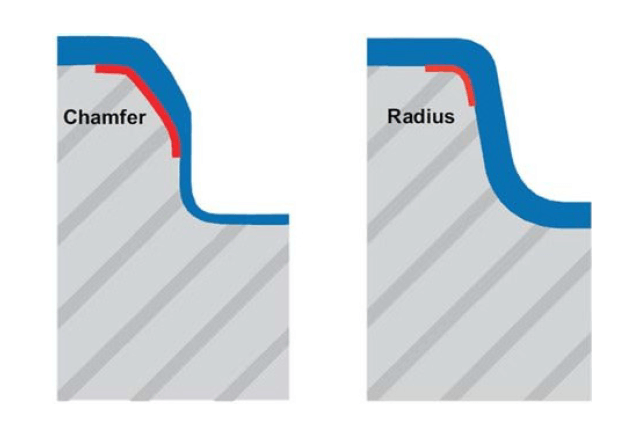
Design Final
Design Padrão TEG
1) Profundidade de bolsa = (altura máxima do produto) + 0,5 mm
2) Raio de selagem= Raio Padrão de 0,5mm
3) Raio de canto= Raio Padrão mínimo de 1mm
4) Ângulo de escoamento:
Materiais de Alta Barreira (ACLAR) à 7 ° -9 °
Materiais não-barreira (PVC / PVDC) a 5 ° -7 °
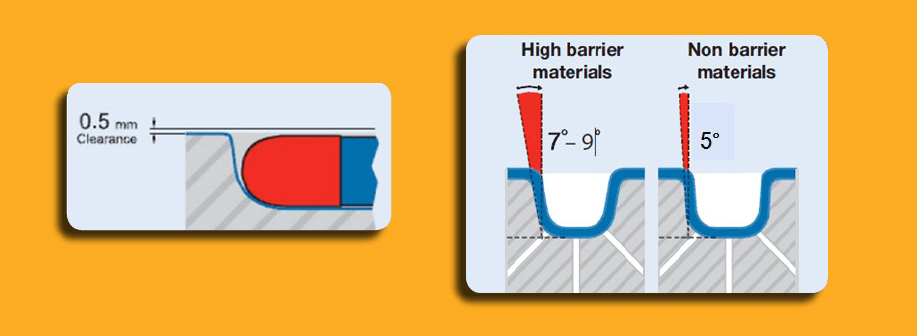
Se o material de formação ficar mais esticado do que deveria, o resultado pode ser o rasgo ou afinamento na base da cavidade, o que resulta numa baixa barreira de proteção para seu produto.

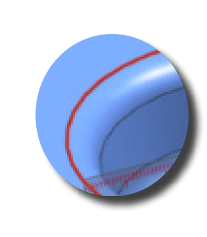
A cavidade e a pré formação da área superior são examinados para verificar a real necessidade de um plug assist.
A TEG usa este cálculo do Deep Draw Ratio para determinar se o plug assist é necessário:
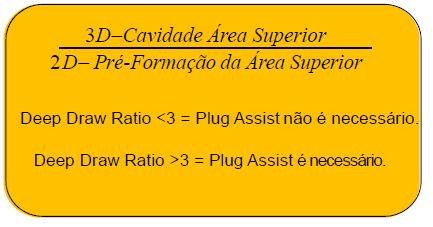
PRÉ-FORMAÇÃO (PLUG ASSIST)
Formação com plug assist
Para saber se o plug assist é necessário você precisa primeiramente seguir a fórmula acima citada, se o deep draw ratio for maior do que 3:1 a pré-formação com plug assist é recomendada.
Tudo o que você precisa fazer é observar os detalhes e analisar o cenário de seus materiais e equipamentos. Sem o real entendimento do cenário como um todo, você encontrará dificuldades no projeto.
Material para formação com Plug
Existe uma variedade de materiais disponíveis para o plug assist de blister farmaêutico, nós recomendamos o uso de materiais isoladores com um baixo coeficiente de atrito como Teflon ®, Delrin®, ou espuma sintática.
Design da formação do Plug Assist
No momento em que for projetar a forma do plug deve se prestar uma atenção especial. A distribuição ideal do material ocorre normalmente com uma penetração de 2/3 de cavidade.
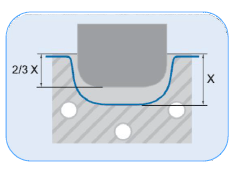
PLUG ASSIST – FORMAÇÃO FRIA
Formato do Plug
O design do formato do plug é crítico para evitar micro rasgos ou o alongamento do material de alumínio. O material normalmente é esticado no máximo até 60 do nível do estresse de rendimento e simulados usando ferramentas de análise FEA.
Material de formação do Plug
Como dito anteriormente, existem diversos materiais que podem ser utilizados no plug, a TEG (nossa representada em ferramentais para embalagens primárias) recomenda o uso de Teflon ®. Ele tem um coeficiente de atrito muito baixo o que significa uma menor força para formação.
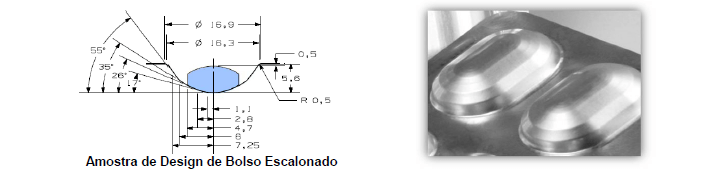
VEDAÇÃO MÍNIMA
Tanto para selagem tipo contínua quanto para a selagem intermitente, usando um padrão de 0.8mm de passo de recartilha, posicionado no meio da diagonal, o correto é ter ao menos 2 passos de recartilha selada, então iremos necessitar de 2.26mm.
Porém, quando colocado 3mm você constrói um fator de segurança adicional, o que é recomendado pela TEG.
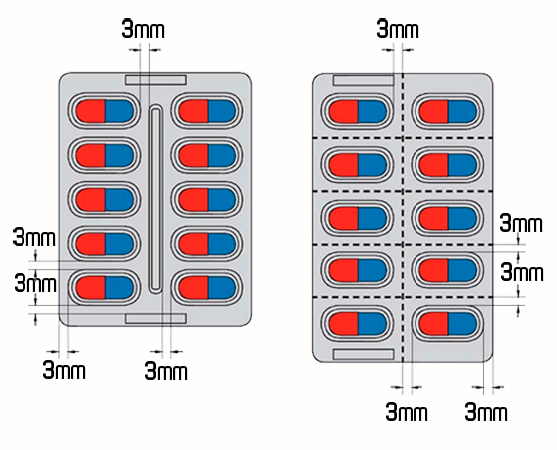
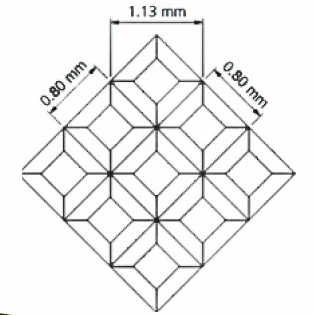
RIGIDEZ MÍNIMA E DESIGN DO NERVO DO BLISTER FARMACÊUTICO
Um blister é a combinação de múltiplos materiais. Cada um destes materiais tem o seu próprio conjunto de propriedades mecânicas e térmicas. Também, cada material tem seu próprio histórico exclusivo para combinação na emblistadora. A maioria dos materiais tem uma tendência de memória (Curvatura) em algum grau.
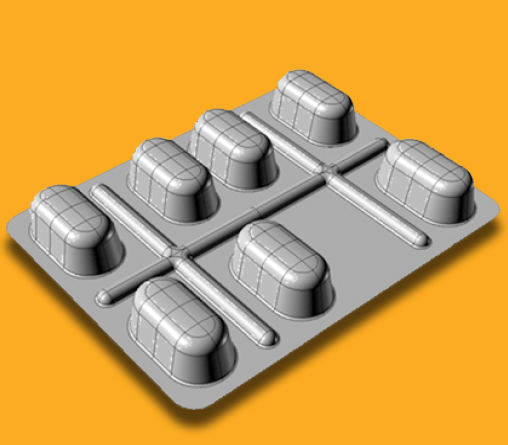
Infelizmente, estas propriedades individuais, memórias e novas variáveis introduzidas pelo processo de alimentação de comprimidos pode oferecer um resultado indesejado e “encanoamento”, geralmente o blister “encanoa” na direção do seu maior lado.
Uma boa regra é minimizar a área sem selagem (ilustração abaixo em vermelho) em um blister, reduzindo a quantidade de calor aplicada no plástico. Adicionar espaço vazio ou nervuras é a melhor maneira para conseguir fazer isso. Nervuras também tem a vantagem de dar resistência na estrutura da bolha, as larguras das nervuras devem estar entre 2-3 vezes a profundidade formada.
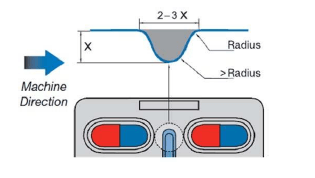
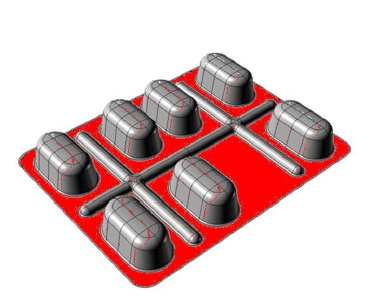
Esses são somente alguns princípios gerais para que você possa entender melhor sobre o design do seu blister e começar a planejar e analisar os seus projetos com outro olhar. Sempre orientamos nossos clientes a ter parcerias com fornecedores que possam lhe ofertar equipamentos de qualidade e que lhe proporcionem soluções para os projetos, ajudando na performance do equipamento e no perfeito desempenho do produto final.
Se você tiver alguma dúvida ou sugestão, por favor, entre em contato conosco e ficaremos felizes em trocar informações.
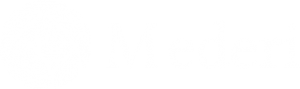
Somos especialistas em equipamentos para a Indústria Farmacêutica.
Entre em Contato
Avenida São João, 2375, Sala 1010São José dos Campos – SPCEP 12242-000
(11) 98470-3068
Seg – Sex: 9AM – 17PM
mederi@mederibrasil.com